- Oprogramowanie
-
Mechanika
- Autodesk AutoCAD LT
- Autodesk AutoCAD
- Autodesk AutoCAD Mechanical
- Autodesk Inventor Professional
- Autodesk Product Design & Manufacturing Collection
- Autodesk AutoCAD Electrical
- Autodesk Viewer
- ProModel AutoCAD Edition
- Autodesk Fusion 360 with PowerMill
- Autodesk Fusion 360 with Netfabb
- Fusion 360 with FeatureCAM
- Autodesk Vault
- Fusion Operations
- Autodesk CFD
- Autodesk Moldflow
- Autodesk Inventor Nastran
- Autodesk Helius PFA
- Autodesk Fusion Cloud
- Autodesk Factory Design Utilities
- ProModel AutoCAD Edition
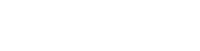
Oprogramowanie ProModel AutoCAD Edition
System wspomagający planowanie i symulację procesów produkcyjnych, zintegrowany z aplikacjami Autodesk.
Zapytaj o cenę: 22 201 91 56 / procad@procad.pl
ProModel zaawansowane narzędzie do planowania
ProModel jest zaawansowanym narzędziem do planowania, symulacji i analizy złożonych procesów produkcyjnych różnego typu. W programie ProModel, zintegrowanym z aplikacjami Autocad i Inventor, możliwe jest opisanie procesu produkcyjnego bezpośrednio na planach przestrzennych zakładu z wykorzystaniem komponentów wyposażenia fabryki, dostępnych w zasobach Autodesk Factory Design Utilities.
Użytkowanie programu cechuje łatwość definiowania zdarzeń w różnych konfiguracjach. Elastyczność systemu w zakresie użycia atrybutów, zmiennych i logiki sterowania parametrami, czyni ten system bardzo efektywnym i skalowalnym do procesów produkcyjnych o różnych strukturach.
ProModel umożliwia inżynieromi menadżerom produkcji testowanie systemu, np. w zakresie wykorzystania zasobów, poziomu zapasów, wydajności i harmonogramu produkcji, przed uruchomieniem rzeczywistego procesu, co powoduje znaczące ograniczenie ryzyka planowanego przedsięwzięcia biznesowego.
-
Stała potrzeba poprawiania efektywności procesów wytwarzania nowych zleceń produkcyjnych, możliwa jest do realizacji identyfikacji w symulacjach ProModel, często ukrytych i trudnych do określenia, kosztownych zdarzeń lub czynności, takich jak:
-
1. Nadprodukcja
wytwarzanie przedmiotów, informacji itp., wcześniej, szybciej lub częściej niż niż wymaga tego marszruta procesu
-
2. Oczekiwanie
bezczynny czas oczekiwania na materiały, sprzęt, personel lub informacje
-
3. Transport
niepotrzebny ruch lub transport przedmiotów lub osób
-
4. Czynność zbędne
niewnoszące wartości dodanej produkt lub usługi
-
5. Nadmiar zapasów
wszelkie zapasy wykraczające poza to, co jest potrzebne, aby dostarczyć tylko to, co jest potrzebne i tylko wtedy, gdy jest to potrzebne
-
6. Zmarnowany ruch
nieefektywne lub niepotrzebne działania operatora lub sprzętu
-
7. Wady
popełnione błędy wymagające kontroli, naprawy lub złomowania wartość produktu lub usługi.
Automatyczne sprawdzanie poprawności i identyfikowanie błędów badanego modelu, ułatwia prawidłowe określenie warunków kompletnej symulacji procesu, przeznaczonej do testowania. Podczas wykonywania obliczeń, możliwe jest obserwowanie mierzonych wielkości, które ostatecznie w różnej formie są prezentowane w raportach po zakończeniu symulacji. Zagregowane dane umożliwiają ocenę i wnioskowanie w zakresie poszczególnych operacji, celem poprawy efektywności całego procesu produkcyjnego.
Funkcje w programie ProModel AutoCAD Edition
Skróć czas i wysiłek w celu uzyskania optymalnego projektu budując swój układ oraz model w programie ProModel AutoCAD.
-
Typowe funkcje wykorzystywane w symulacjach realizowanych z wykorzystaniem programu ProModel:
-
Assembly Lines
produkcja realizowana w planowanych marszrutach z wykorzystaniem dostępnych zasobów zakładu
-
Job Shops
realizacja zleceń produkcyjnych na podstawie aktualnych zamówień
-
JIT and KANBAN
metoda zarządzania procesem produkcyjno-magazynowym, mająca na celu redukcję pracy w toku i poziomu zapasów
-
Flexible Manufacturing Systems
elastyczny system produkcji, umożliwiający dostosowanie przepływu materiałów i wykorzystania maszyn do zmian zleceń produkcyjnych
-
Supply Chain Logistics
metoda zarządzania procesem produkcyjno-magazynowym, mająca na celu redukcję pracy w toku i poziomu zapasów
-
Flexible Manufacturing Systems
elastyczny system produkcji, umożliwiający dostosowanie przepływu materiałów i wykorzystania maszyn do zmian zleceń produkcyjnych
-
Six Sigma
pozyskiwanie i analiza danych w celu identyfikacji błędów jeszcze przed ich wystąpieniem, co umożliwia osiągnięcia wysokiej jakości produktu i ograniczenia kosztów produkcji.
Pracuj zgodnie z logiką działań technologicznych
ProModel postrzega system produkcyjny jako układ miejsc przetwarzania, takich jak maszyny i stacje robocze, w których wykonywane są czynności zgodnie z logiką działań technologicznych, realizujących proces wytwarzania. System ProModel, obejmuje również analizą ścieżki przepływu jednostek i zasobów oraz komponenty pomocnicze modelu, takie jak operatorzy i sprzęt do przenoszenia i transportu materiałów.
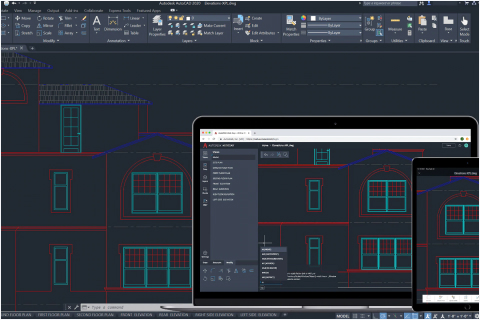
Określ warunki i sposób przeprowadzenia badania
Po zidentyfikowaniu celów biznesowych symulacji, należy określić warunki i sposób przeprowadzenia badania. Nie ma ścisłych zasad i procedur badania symulacyjnego, jednak ogólnie przyjmuje się wytyczne i zalecenia opisane w literaturze (Shannon, 1975; Gordon, 1978; Law, 1991):
1. Planowanie badania
2. Definiowanie systemu
3. Budowanie modelu
4. Obliczenia i symulacje
5. Analiza danych
6. Raport wyników.
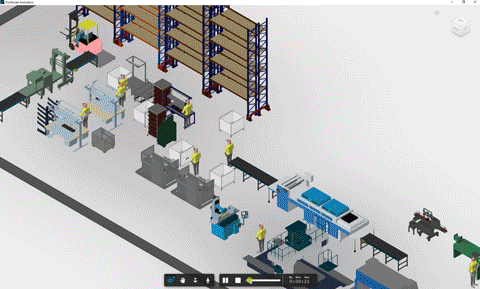
-
Planowanie badania – do przykładowych celów w planowaniu badania symulacyjnego możemy zaliczyć:
-
Analiza wydajności
ocena systemu pracującego w określonych warunkach wg. kryteriów wykorzystania zasobów, przepustowości, czasu oczekiwania, itp.
-
Analiza pojemności
identyfikacja maksymalnej wydajności i produkcyjności systemu
-
Analiza możliwości
jak zmiany w zakresie np. zasobów, przepływu materiałów, zwiększenia siły roboczej, wpływają na oczekiwaną wydajność, czas oczekiwania, itp.
-
Analiza możliwości
jak zmiany w zakresie np. zasobów, przepływu materiałów, zwiększenia siły roboczej, wpływają na oczekiwaną wydajność, czas oczekiwania, itp.
-
Badanie porównawcze
ocena wariantów i konfiguracji modelu
-
Analiza wrażliwości
które zmienne i parametry mają największy, i jaki wpływ na jedną lub więcej miar wydajności systemu
-
Badanie optymalizacji
szukanie kombinacji wartości dla danego zestawu zmiennych, umożliwiających osiągnięcie określonych celów wydajności
-
Analiza decyzji/odpowiedzi
szukanie kombinacji wartości dla danego zestawu zmiennych, umożliwiających osiągnięcie określonych celów wydajności
-
Analiza ograniczeń
identyfikowanie ograniczenia i „wąskich gardeł” oraz czynników umożliwiających ich zmniejszenie lub wyeliminowanie
-
Skuteczność komunikacji
jakie zmienne i reprezentacje graficzne można wykorzystać do najefektywniejszego zobrazowania dynamicznego zachowania lub działania systemu.
ProModel, integruje się z aplikacjami Autodesk serii: 2019, 2020, 2021, 2022, 2023 i 2024. ProModel AutoCAD Edition, wymaga aplikacji: AutoCAD IST ProModel AutoCAD Edition and 3D Animator, wymaga oprogramowania Inventor Professional z rozszerzeniem Factory Design Utilities, dostępnego w pakiecie aplikacji Autodesk Product Design and Manufacturing Collection. |
|
Komputer i procesor: |
Procesor 64-bitowy (x86-64) |
Pamięć: |
2 GB pamięci RAM (64-bit) |
Dysk twardy: |
15 GB wolnego miejsca na dysku |
System operacyjny: |
Windows 10, 11 |
Inne: |
Dostęp do Internetu (w celu rejestracji i aktualizacji online) |
Pełna lista oprogramowania
AutoCAD
- AutoCAD LT
- AutoCAD
- AutoCAD Electrical
- AutoCAD Mechanical
- AutoCAD Map 3D
- Autodesk AutoCAD P&ID
- AutoCAD Architecture
- Autodesk AutoCAD Plant 3D
Inżynieria Lądowa i Infrastruktura
Architektura
- Autodesk Revit
- Autodesk AEC Collection
- AutoCAD Revit LT Suite
- Autodesk Nawisworks
- Autodesk Spacemaker
- Autodesk FormIt PRO
- Autodesk AutoCAD Architecture
Projektowanie Procesów Technologicznych
Konstrukcje
Rozwiązania chmurowe
Instalacje inżynierski
Oprogramowanie CAD - 3D
Oprogramowanie CAD - 2D
Zarządzanie dokumentacją
Oprogramowanie CAE
Oprogramowanie CAM
Animacja 3D i Modelowanie
Wizualizacja
Produkcja filmowa i telewizyjna