- Oprogramowanie
-
Mechanika
- Autodesk AutoCAD LT
- Autodesk AutoCAD
- Autodesk AutoCAD Mechanical
- Autodesk Inventor Professional
- Autodesk Product Design & Manufacturing Collection
- Autodesk AutoCAD Electrical
- Autodesk Viewer
- ProModel AutoCAD Edition
- Autodesk Fusion 360 with PowerMill
- Autodesk Fusion 360 with Netfabb
- Fusion 360 with FeatureCAM
- Autodesk Vault
- Fusion Operations
- Autodesk CFD
- Autodesk Moldflow
- Autodesk Inventor Nastran
- Autodesk Helius PFA
- Autodesk Fusion Cloud
- Autodesk Factory Design Utilities
- Autodesk Moldflow
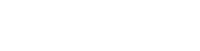
Oprogramowanie Autodesk Moldflow
Zapytaj o cenę: 22 201 91 56 / procad@procad.pl
Najdłużej istniejące na rynku rozwiązanie do symulacji tworzyw
Oprogramowanie Moldflow jest najbardziej rozwiniętym i najdłużej istniejącym rozwiązaniem na rynku. Przez prawie 50 lat rozwoju oprogramowania, jego nazwa stała się synonimem tego typu programów – dla większości inżynierów z branży tworzyw sztucznych, wyrażenie „analiza Moldflow” oznacza symulację komputerową typu CAE modelu wypraski, formy czy procesu przetwórstwa.
-
Największa baza danych materiałowych
Bez danych materiałowych ani rusz – program posiada w swojej bazie niezbędne informacje reologiczne, mechaniczne i termiczne dla ponad 11 tys. gatunków tworzyw sztucznych, dzięki czemu możliwe jest realizowanie symulacji dla wszystkich branż. Baza obejmuje również silikony, elastomery termoplastyczne oraz tworzywa termoutwardzalne.
-
Uznane narzędzie w branży motoryzacyjnej
Oprogramowanie Autodesk Moldflow jest cenionym narzędziem stosowanym z powodzeniem w branżach stawiających wypraskom najwyższe wymagania pod względem jakości powierzchni i dokładności kształtu – przede wszystkim w branży automotive, AGD i elektrotechnicznej.
-
Symulacje wszystkich liczących się technologii specjalnych
Program posiada dedykowane wszystkich liczących się technologii specjalnych wtryskiwania. Pozwala na symulację następujących procesów przetwórczych: wtryskiwanie sekwencyjne, obtryskiwanie zaprasek, wtryskiwanie dwukomponentowe i wielokomponentowe, wtryskiwanie sandwiczowe, wtryskiwanie z gazem, wtryskiwanie silikonów, wtryskiwanie reaktywne, spienianie fizyczne i spienianie chemiczne.
-
Teraz dwa sposoby licencjonowania
Oprogramowanie Autodesk Moldflow jest aktualnie dostępne w dwóch wersjach licencjonowania – jednostanowiskowej oraz sieciowej. Dobierz wersję oprogramowania do potrzeb swojego przedsiębiorstwa.
Zawartość
-
Licencja Fusion 360 w cenie
- W ramach licencji oprogramowania Autodesk Moldflow jest dostępna licencja Fusion 360. (logo fusion360 oraz link do fusion)
- W ramach licencji oprogramowania Autodesk Moldflow jest dostępna licencja Fusion 360. (logo fusion360 oraz link do fusion)
-
Autodesk HeliusW przypadku wersji Insight Ultimate i Insight Named Account dostępny jest również program Autodesk Helius do uwzględnienia właściwości tworzyw w symulacjach wytrzymałościowych wyprasek.
Funkcje w programie Moldflow
Autodesk Moldflow Insight to flagowy produkt Autodesk, który w stosunku do wersji „doradczej”, jakim jest wariant Autodesk Moldflow Adviser, stanowi znacznie silniejsze narzędzie analityczno-optymalizacyjne.
Możliwość symulacji częściowego i pełnego cyklu procesu wtryskiwania
Oprogramowanie umożliwia przeprowadzenie obliczeń zarówno częściowego jak i pełnego cyklu procesu wtryskiwania – zależnie od stopnia zaawansowania projektu. Pozwala to na optymalizację geometrii wypraski oraz lokalizacji punktu wtrysku przed przystąpieniem prac do konstrukcji formy wtryskowej.
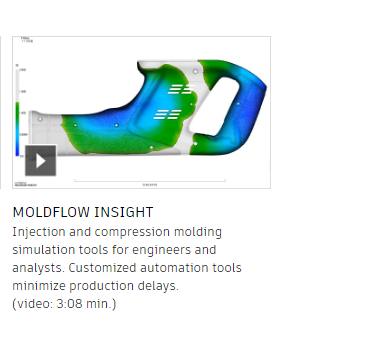
Automatyczna kompensacja skurczu
Program na podstawie przeprowadzonych symulacji wskazuje proponowaną wielkość skurczu, żeby zminimalizować deformacje wypraski.
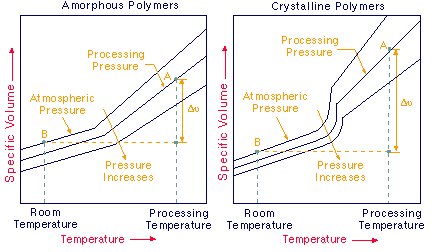
-
Trzy rodzaje siatek obliczeniowych
Oprogramowanie korzysta z trzech rodzajów siatek doobliczeń (dwie dedykowane do wyrobów cienkościennych, jedną do wyrobów grubościennych). Siatka Dual Domain® jest opatentowaną technologią dostępną tylko w oprogramowaniu Autodesk Moldflow, która bardzo dobrze radzi z elementami cienkościennymi przy zachowaniu krótkiego czasu oblicze.
-
Generowanie przeciwkształtów
Oprogramowanie Autodesk Moldflow posiada możliwość generowania tzw. przeciwkształtów, czyli kształtów o deformacji w kierunku przeciwnym do uzyskanej w wyniku symulacji. Co ważne, możliwe jest wygenerowanie przeciwkształtu nie tylko w formacie *.STL, ale również w formatach bryłowych *.STEP i *.SAT
Bogate wyniki symulacji
Program jest w stanie dostarczyć bardzo wiele informacji istotnych dla konstruktorów i technologów:
- Rozkład ciśnienia w gnieździe
- Lokalizację linii łączenia
- Zapadnięcia
- Deformacje wyprasek we wszystkich kierunkach
- Efektywność chłodzenia
- Hot-spoty
Wymagania systemowe – Moldflow
System operacyjny |
System operacyjny Windows, 64-bitowy |
Pamięć |
4 GB lub wyższa |
Przestrzeń na dysku |
20 GB lub wyższa |
Przeglądarka internetowa |
Internet Explorer 11.0 or later |
Pełna lista oprogramowania
AutoCAD
- AutoCAD LT
- AutoCAD
- AutoCAD Electrical
- AutoCAD Mechanical
- AutoCAD Map 3D
- Autodesk AutoCAD P&ID
- AutoCAD Architecture
- Autodesk AutoCAD Plant 3D
Inżynieria Lądowa i Infrastruktura
Architektura
- Autodesk Revit
- Autodesk AEC Collection
- AutoCAD Revit LT Suite
- Autodesk Nawisworks
- Autodesk Spacemaker
- Autodesk FormIt PRO
- Autodesk AutoCAD Architecture
Projektowanie Procesów Technologicznych
Konstrukcje
Rozwiązania chmurowe
Instalacje inżynierski
Oprogramowanie CAD - 3D
Oprogramowanie CAD - 2D
Zarządzanie dokumentacją
Oprogramowanie CAE
Oprogramowanie CAM
Animacja 3D i Modelowanie
Wizualizacja
Produkcja filmowa i telewizyjna