- Oprogramowanie
-
Budownictwo
- PROCAD Revit Akcelerator - Karty Mieszkań
- Autodesk Robot Structural Analysis
- Autodesk Advance Steel
- Autodesk AutoCAD LT
- Autodesk AutoCAD
- Autodesk Revit
- Autodesk AEC Collection
- Autodesk AutoCAD Architecture
- Autodesk AutoCAD Electrical
- Autodesk AutoCAD Revit LT Suite
- Autodesk Viewer
- Autodesk Drive
- Autodesk Infraworks
- Autodesk AutoCAD Plant 3D
- PROCAD ReviTEKA LT
- PROCAD ReviTEKA
- Autodesk Nawisworks
- AutoCAD Architecture
- Autodesk Construction Cloud
- Autodesk AutoCAD P&ID
- Autodesk AutoCAD Map 3D
- Autodesk Vehicle Tracking
- Autodesk Docs
- Autodesk Forma (wcześniej Spacemaker)
- Autodesk Civil 3D
- Autodesk FormIt PRO
- Autodesk BIM Collaborate
- Autodesk BIM Collaborate Pro
- Autodesk Build
- Autodesk Takeoff
- Autodesk Nawisworks
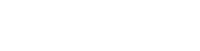
Oprogramowanie Autodesk Nawisworks
Autodesk Navisworks to narzędzie do weryfikacji i koordynacji modeli BIM. Oferuje wspólne środowisko dla modeli pochodzących z wielu źródeł, przegląd kolizji międzybranżowych i narzędzia analizy modelu 3D.
Wykrywanie kolizji międzybranżowych
Autodesk Navisworks umożliwia wykrywanie kilku typów kolizji pomiędzy elementami wczytanych modeli 3D. Są to kolizje twarde z zadaną tolerancją, minimalne prześwity między wskazanymi typami obiektów, oraz duplikaty obiektów. Funkcja umożliwia nadzór nad kolizjami poprzez określenie ich statusu, oraz raportowanie informacji do plików txt, html, xml. Funkcja dostępna wyłącznie w wersji Navisworks MANAGE.
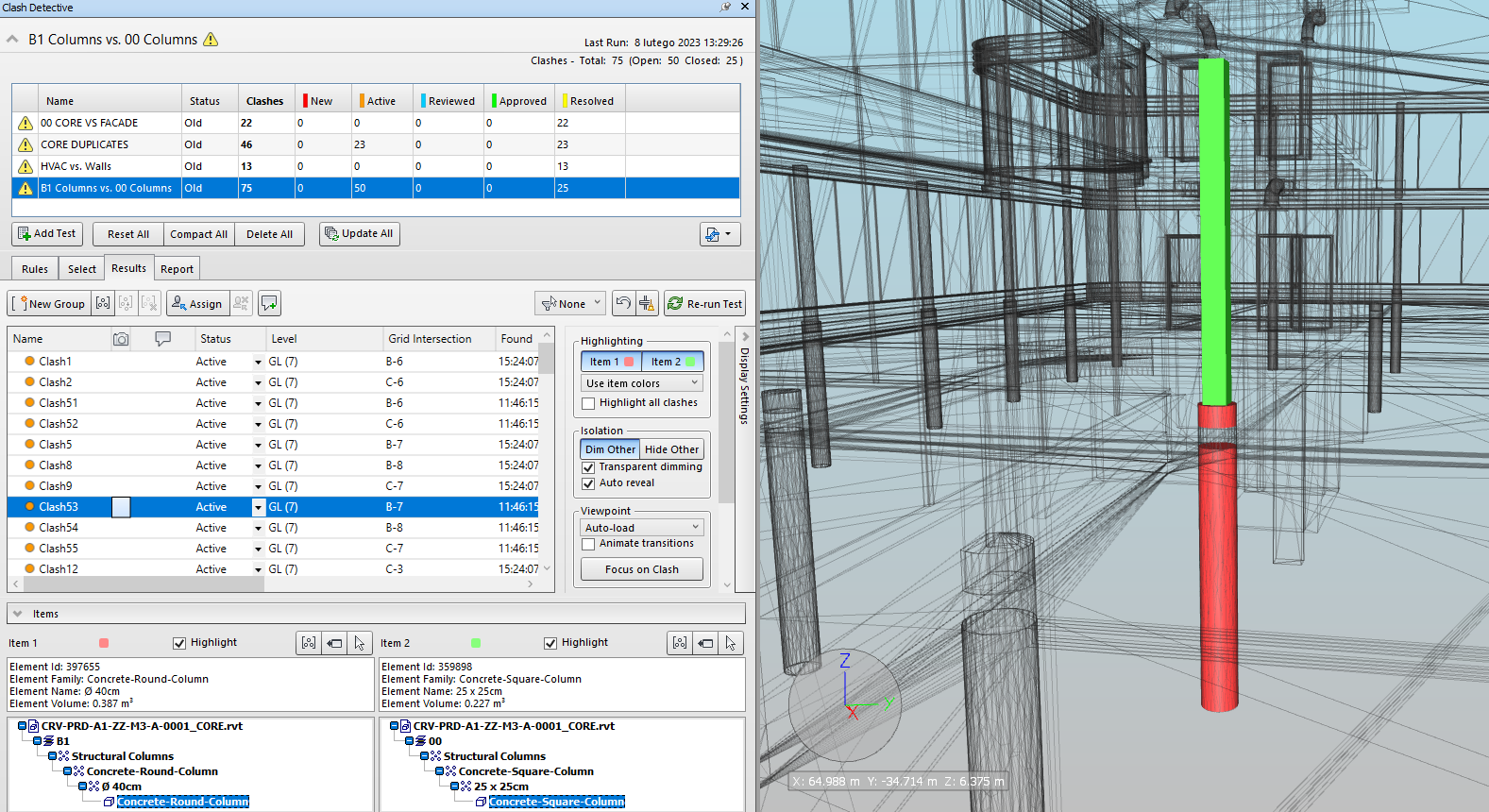
Tworzenie Harmonogramu 4D
Narzędzie Time Liner umożliwia tworzenie wykresu Gantta dla modelu 3D. Dodaj przedział czasowy przewidywany na wykonanie wybranego etapu i uzyskaj animowaną symulację budowy. Narzędzie integruje się z plikami MS Project, CSV oraz Primavera. Dodaj informację o kosztach materiałów i robocizny a uzyskasz symulację 5D.
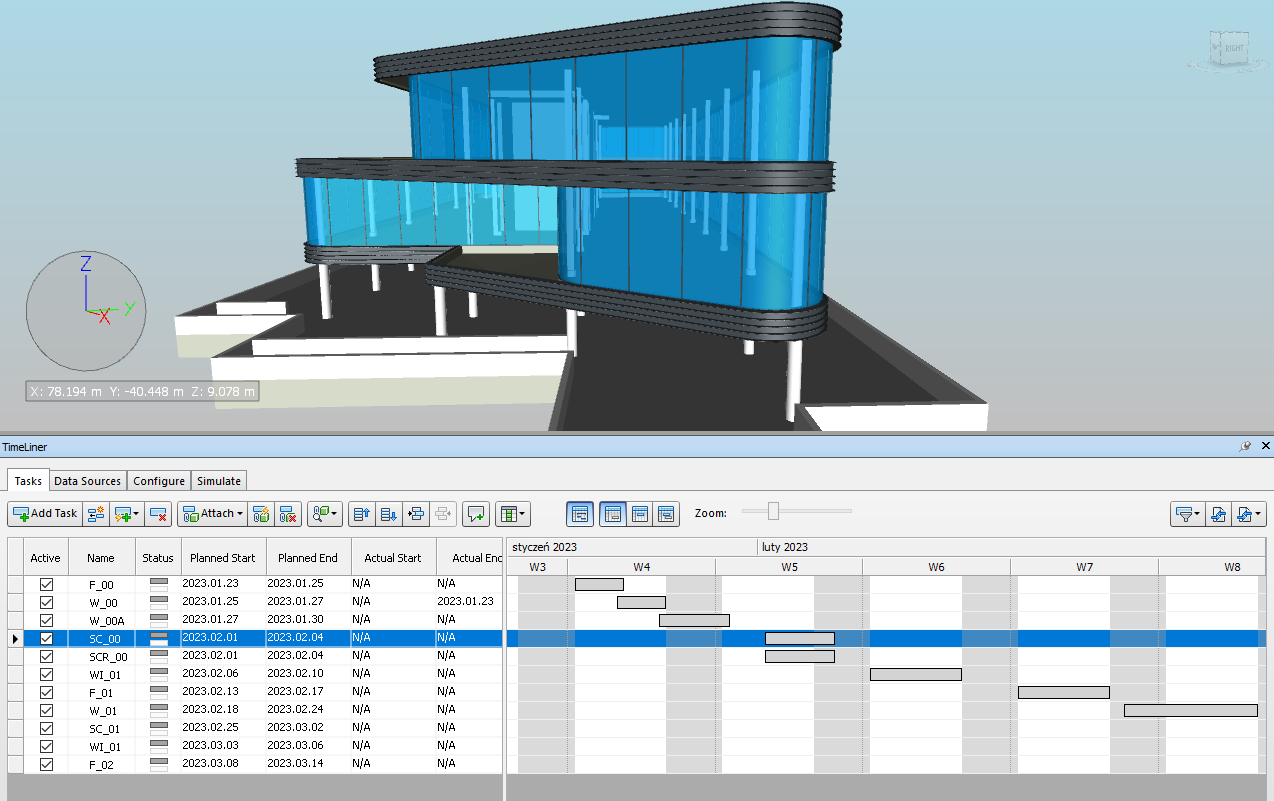
Przedmiary
Moduł Quantification pozwala na zliczanie materiałów zarówno z arkusza (długość, pole powierzchni, ilość) jak również z modelu 3D (długość, szerokość, wysokość, powierzchnia, objętość, ilość ). Narzędzie daje możliwość konfiguracji własnej struktury przedmiaru, oraz wyświetlania modelu według przedmiarowanych obiektów.
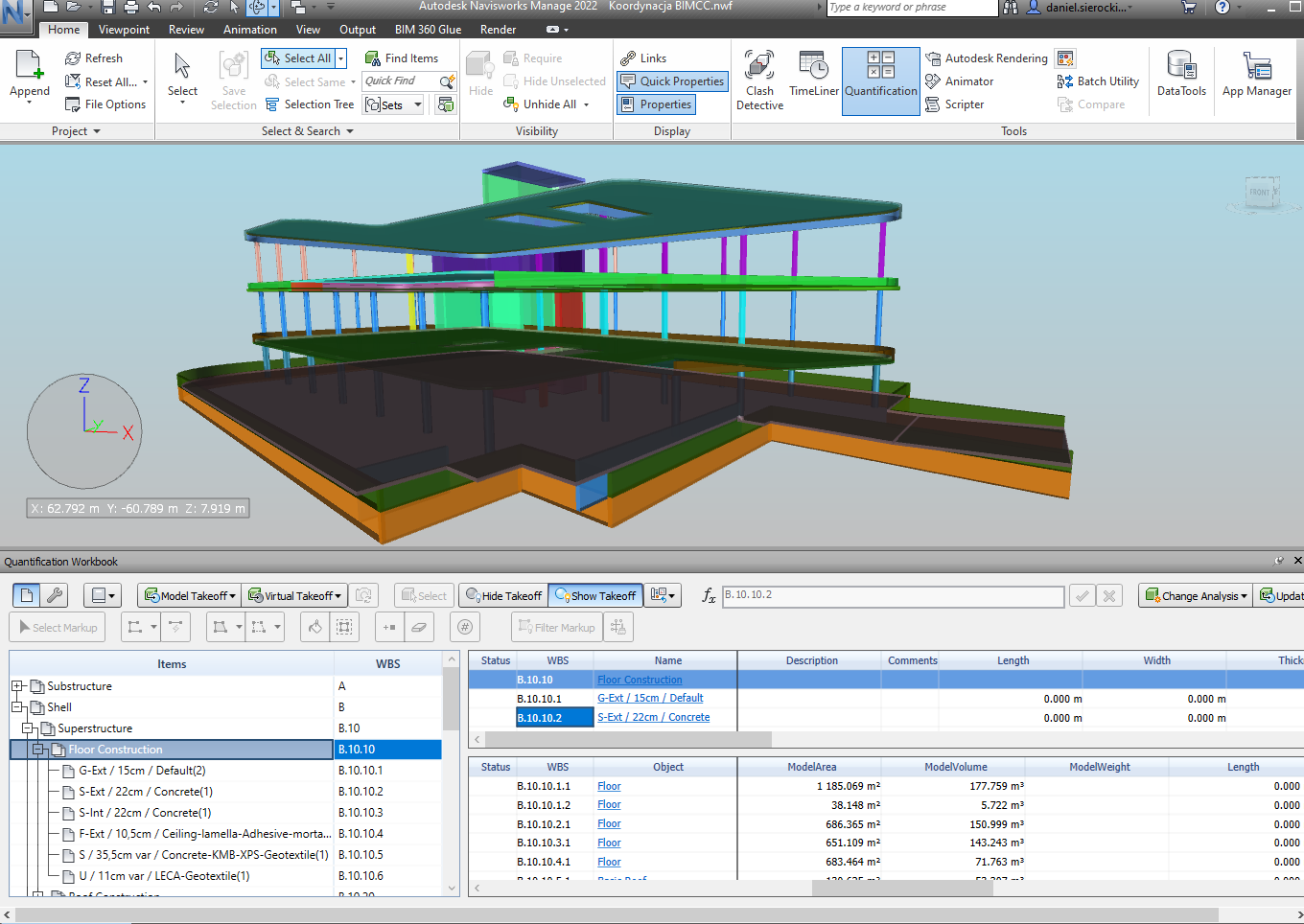
Rendering
Tworzenie wizualizacji w środowisku Nawisworks oparte jest na bibliotece materiałów Autodesk. Program umożliwia użycie funkcji Render in Cloud aby cały proces przeprowadzić bez obciążania zasobów sprzętowych. Efektem renderingu może być obraz statyczny, lub panorama 360 stopni
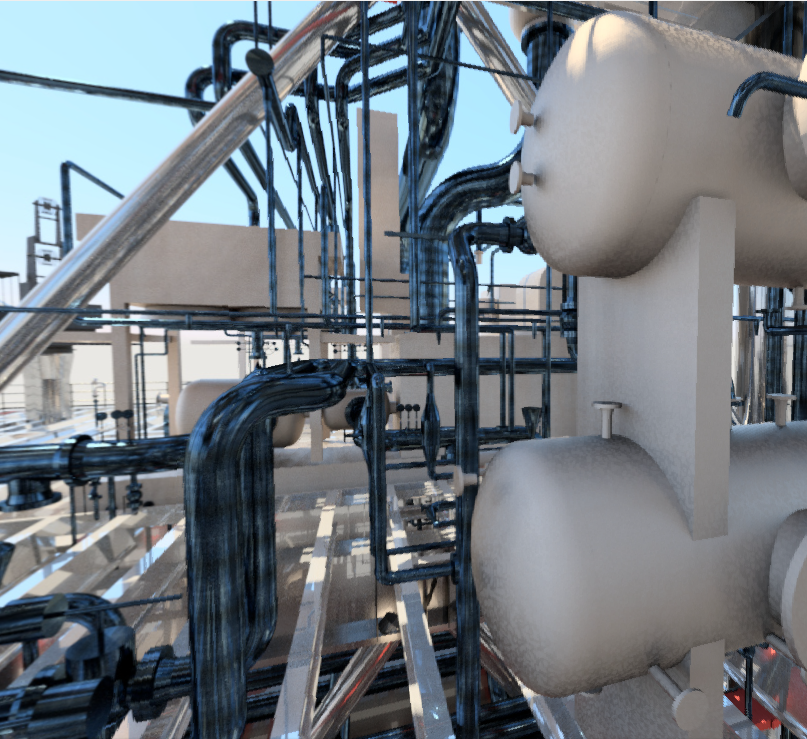
Animacje
Stwórz animację opartą na dowolnym modelu 3D. Spacer po obiekcie, symulacja działania urządzenia, etapy budowy, montaż urządzenia. Wbudowane narzędzie umożliwia animowanie obiektów 3D poprzez określenie stanu początkowego, końcowego oraz transformacji. Do dyspozycji są zmiany przezroczystości, skalowanie obiektów, ruch liniowy, obrót, zmiana koloru oraz ruch kamery.
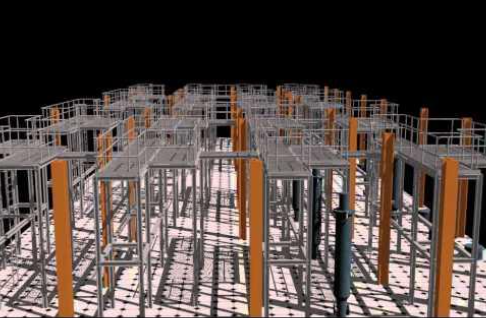
Appearance Profiler
Nadpisz kolory całego modelu według ustalonych kryteriów wyszukiwania, aby lepiej zobrazować odpowiednie kategorie elementów.
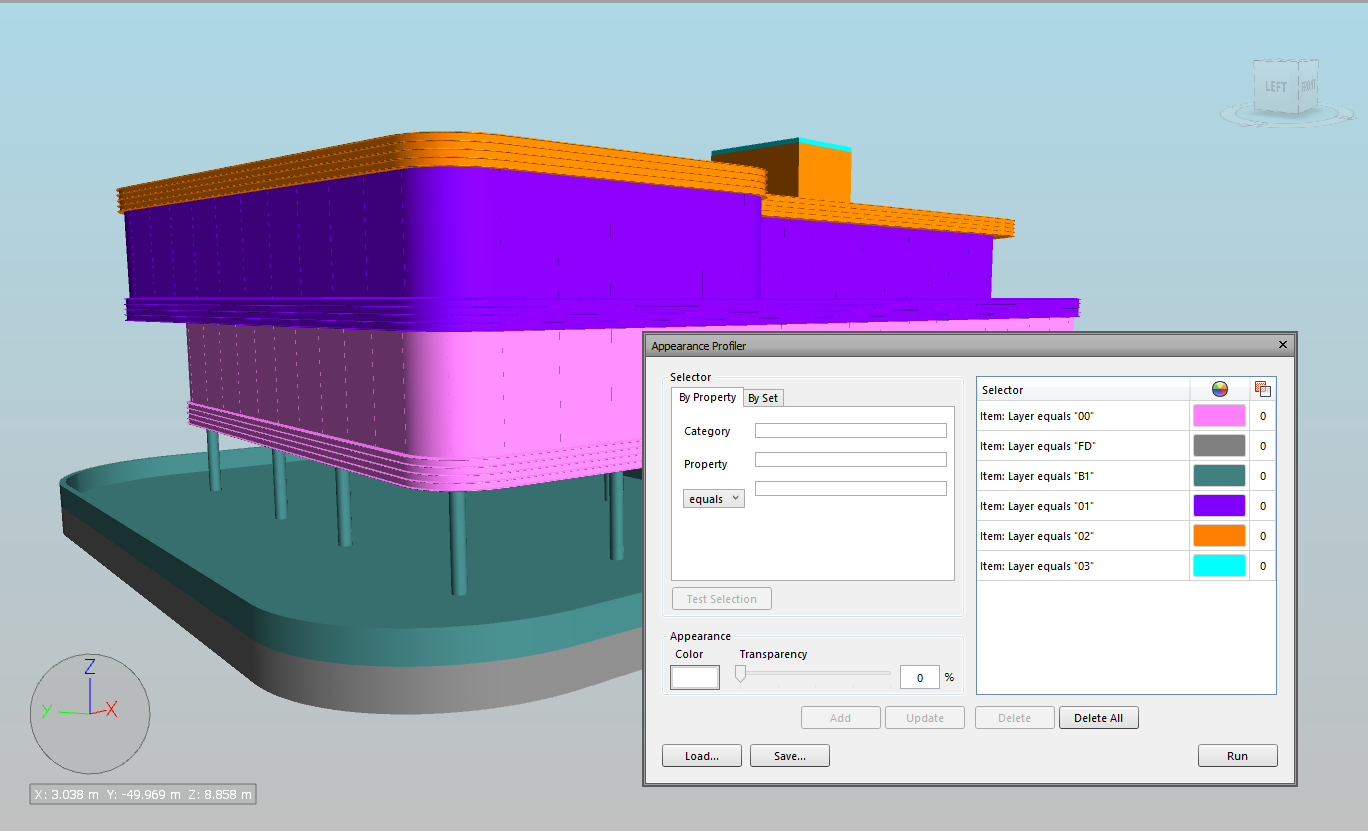
Funkcje w programie Autodesk Navisworks
Autodesk Navisworks to narzędzie do weryfikacji i koordynacji modeli BIM. Oferuje wspólne środowisko dla modeli pochodzących z wielu źródeł, przegląd kolizji międzybranżowych i narzędzia analizy modelu 3D.
Przegląd wybranych funkcji
Przegląd wybranych funkcji znajduje się w materiale video
Najnowsze terminy szkoleń
Autodesk Navisworks
Pokaż cenę
Pokaż cenę
Terminy zajęć
18.09.2025r. (08:30-15:30)
Miejsce szkolenia
Kurs Online
tel. (58) 739-68-00
Cena
Online netto | 799,00 zł |
Online brutto | 982,77 zł |
Studencka online netto | 451,22 zł |
Studencka online brutto | 555,00 zł |
Nasze cechy i wartości

Blisko klienta (5 oddziałów)
Jesteśmy blisko Ciebie i Twojego biznesu. Oddziały: Gdańsk, Warszawa, Katowice, Poznań, Radom.

60-ciu profesjonalistów w zespole PROCAD

50.000 przeszkolonych profesjonalistów

8h dziennie bezpłatnego wsparcia technicznego

Usługi dopasowane do biznesu

Baza wiedzy

1300 unikalnych filmów instruktażowych

Certyfikat Pochodzenia Oprogramowania
Wymagania systemowe Navisworks Manage/Simulate/Freedom
Minimum:
System operacyjny |
64-bitowy system operacyjny Microsoft® Windows® 11 i Windows 10. |
Procesor |
Procesor 3,0 GHz lub szybszy |
Pamięć |
2 GB RAM (minimum) |
Miejsce na dysku |
15 GB wolnego miejsca na dysku na instalację |
Grafika |
Karta graficzna obsługująca Direct3D 9® i OpenGL® z Shader Model 2 (minimum) |
Wyświetlacz |
Wyświetlacz VGA 1280 x 800 z prawdziwymi kolorami (zalecany monitor 1920 x 1080 i 32-bitowy adapter do wyświetlania wideo) |
Produkty komplementarne
Pełna lista oprogramowania
AutoCAD
- AutoCAD LT
- AutoCAD
- AutoCAD Electrical
- AutoCAD Mechanical
- AutoCAD Map 3D
- Autodesk AutoCAD P&ID
- AutoCAD Architecture
- Autodesk AutoCAD Plant 3D
Inżynieria Lądowa i Infrastruktura
Architektura
- Autodesk Revit
- Autodesk AEC Collection
- AutoCAD Revit LT Suite
- Autodesk Nawisworks
- Autodesk Spacemaker
- Autodesk FormIt PRO
- Autodesk AutoCAD Architecture
Projektowanie Procesów Technologicznych
Konstrukcje
Rozwiązania chmurowe
Instalacje inżynierski
Oprogramowanie CAD - 3D
Oprogramowanie CAD - 2D
Zarządzanie dokumentacją
Oprogramowanie CAE
Oprogramowanie CAM
Animacja 3D i Modelowanie
Wizualizacja
Produkcja filmowa i telewizyjna